3D printing is a new manufacturing technology that turns CAD models into physical parts. It can create complex parts that would be impossible to make through traditional means.
The most common 3D printers use a technique called Fused Deposition Modeling. This method uses a heat-resistant plastic like ABS to lay down layer after layer of material. Contact By3Design now!
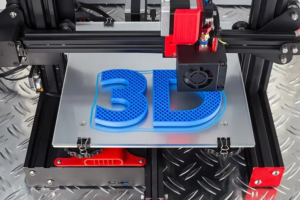
With rapid prototyping, or 3D printing, designers can go from CAD design to holding a physical prototype. This process cuts development time and can help avoid costly mistakes.
There are various types of rapid prototyping methods, all designed to suit different needs. One example is FDM, which uses a printer with a nozzle that can dispense either a wax or plastic-like polymer to create the layers needed for the final product. The nozzle can be moved around the product to shape it and build it up. The layers are then fused together using heat, and the process can be repeated until the desired product is complete.
Another popular technique is Stereolithography (SLA). This process utilizes a laser to solidify a digital CAD model in a vat of resin, layer-by-layer. It’s a popular option for visual models and medical or dental prototypes. The resulting product may be clear, transparent, or opaque and can include intricate details. For industrial-grade or functional prototypes, there are other options such as injection molding, CNC machining and vacuum casting.
These methods can be used for end-use parts, as well as jigs and fixtures. Many industries, including the automotive industry, now use these tools for rapid manufacturing. They can produce spare parts or short-run custom manufactured components without having to invest in expensive molds. This can also reduce stock levels and shave off production times.
Prototypes are also helpful for gaining buy-in from stakeholders. The ability to quickly and inexpensively iterate a product gives people an idea of how the finished product will look, feel, and function before investing in a full production run. This can be especially useful when working with a new or complicated product that requires extensive testing.
When a prototype is complete, it can be used to conduct physical tests to ensure that the design meets or exceeds requirements. This helps to identify flaws in the design that would otherwise be difficult or impossible to discover, saving valuable time and money. This can be especially beneficial for complex products that could take weeks or months to produce using conventional processes.
Rapid Manufacturing
Using 3D printing, engineers can create high-fidelity prototypes that accurately represent the final product. This helps to identify flaws in the design early on and prevent costly revisions once production begins.
Creating an object using 3D printing starts with a digital model of the desired product, normally created through computer aided design (CAD) software. This is then converted into a file format that can be read by the 3D printer, and then loaded onto the machine to start building the object.
There are several different types of 3D printers used to create products, the most popular being fused deposition modeling (FDM) and stereolithography (SLA). FDM uses a heated nozzle to extrude layers of liquid plastic over a base layer, forming the shape of the product. SLA uses ultraviolet light to cure liquid resin on top of a powdered substrate, resulting in strong and accurate prints.
Another type of printing known as direct metal laser sintering (DMLS) is also becoming increasingly popular. This process is similar to SLA, but instead of using a layering method, the metal granules are placed on top of each other and then treated with a laser that fuses them together into a solid part. While there are many benefits to leveraging 3D printing in manufacturing, one of the main advantages is that it cuts out the need for tooling, reducing the overall cost of production. Additionally, the ability to customize products makes it easier for manufacturers to meet specific customer demands and needs. This can be a life-changing benefit in certain cases, such as when it comes to obstetric and prosthetic devices or medical equipment.
Having an in-house 3D printer allows manufacturers to take a more iterative approach when designing products, making changes instantly and dramatically reducing the time it takes to go from digital design to holding a physical prototype in your hand. Ultimately, this can help companies to bring their new products to market faster than their competition. It’s been said that “time is money” and it seems that with 3D printing, this saying is especially true.
Additive Manufacturing
The 3D printing process, or additive manufacturing, is a construction method that builds up objects from a CAD model or 3D scan using a variety of materials, including plastics, composites and even bio-materials. It is accomplished through a process of layering whereby powder grains, liquids or solids are deposited, joined or fused together under computer control, typically in a vertical direction and layer by layer. The result is a complete three-dimensional object that may be rigid or flexible, depending on the material used and the fabrication technique employed.
The popularity of additive manufacturing is largely due to the ability to create complex shapes with ease that could not be produced in conventional ways. For example, the additive manufacturing process can create overhangs and microchannels in components that are impossible or extremely difficult to produce with traditional subtractive methods. This opens up new design possibilities that would not be possible with conventional techniques and enables manufacturers to consolidate assemblies into fewer parts for lower costs and less weight, increasing functionality and speeding up production times.
Modern additive manufacturing processes include sintering, melting and stereolithography, among others. They are also capable of producing a wide range of colors and textures, and have become popular with hobbyists for their low cost, user-friendly features.
As the technology evolves, a rethinking of how products are made is emerging. Rather than manufacturing them in large batches for distribution globally, companies are creating products and generating replacement parts on demand as they are needed, bypassing supply-chain bottlenecks. This is akin to commons-based peer production, an alternative business model that relies on sharing infrastructure costs and localized economies of scale.
Additive manufacturing is also lowering the barrier to entry for new designers and entrepreneurs, making it easier and more affordable to make unique products. This has opened the door for new product categories, such as bespoke, made-to-measure devices, which can be created quickly with a digital file matched to an actual body scan. For example, hearing aids can now be printed to fit each individual patient. It has also enabled the rail industry to replace aging train couplings with a customised version in a matter of weeks, reducing maintenance and repair costs.
Additive Materials
As the name indicates, additive manufacturing processes use a layer-by-layer process to create parts and products. The material that makes up each layer is deposited or fused together using the printer’s dedicated apparatus. The type of material used depends on the printer, its process, and what end product is desired. The most established types of printing machines include stereolithography, selective laser sintering (SLS), and fused deposition modeling (3D printed plastic). These systems are generally used by professional manufacturers and hobbyists alike.
Other additive manufacturing technologies, such as multijet printing, direct energy deposition, and laser sintering with liquid binding, work in much the same way by depositing or fusing layers of material onto an object. The difference between these processes and the 3D printing techniques mentioned previously is that they use different materials. These materials are typically specialized to perform within the specific apparatus of each additive manufacturing process. The system manufacturer typically distributes these materials to its user community.
The most common materials used in 3D printing are polymers, metals and ceramics. These materials are used in medical, automotive and aerospace applications for their strength and design flexibility. The most commonly used polymers are acrylonitrile butadiene styrene (ABS), polylactic acid (PLA) and polycarbonate. Other polymers include nylon and thermoplastic elastomers, as well as water-soluble polyvinyl alcohol. Metals are also a widely used additive manufacturing material, particularly for aerospace and automotive applications, due to their durability and strength. Metal AM works differently than plastic printing as the melt temperature of metal is too high to accommodate an extruder. In order to print with metal, the material must be presented as a powder and converted to a solid through heat, either by lasering or sintering in an oven.
The versatility of additive manufacturing allows it to be used in virtually any industry. Companies can quickly and easily develop prototypes of new products that look and function like their final versions, reducing the risk of expensive revisions or costly tooling changes down the line. Those prototypes can be tested for usability and functionality, as well as analyzed for manufacturability. In addition, 3D printing can make spare parts more readily available and decrease the need for large warehousing facilities.